На 3D-принтері надрукували міцний сплав, який збільшить вироблення енергії турбінними генераторами з меншим викидом вуглецю.
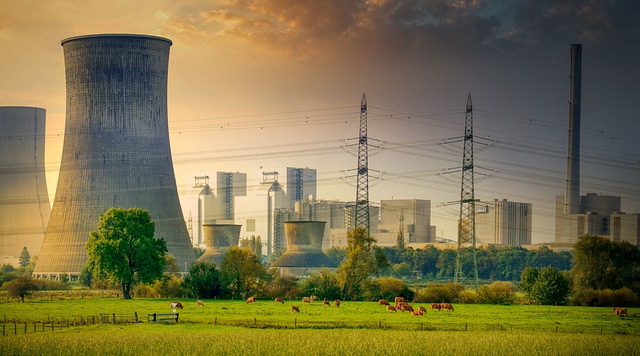
Американські інженери використовували 3D-принтер для створення високоефективного металевого сплаву (суперсплаву) з незвичайним складом. Він міцніше, легше і витримує більш високі температури, ніж сучасні матеріали, використовувані для створення турбін. Технологія підвищить виробництво енергії на електростанціях, що працюють від викопного палива і АЕС.
Вчені використовували 3D-принтер, щоб швидко розплавити порошкоподібні метали, а потім роздрукувати зразок суміші. Готовий сплав включає 42% алюмінію, 25% титану, 13% ніобію, 8% цирконію, 8% молібдену і 4% танталу. Дослідження показало, що при температурі 800 °C склад міцніший, ніж багато інших високоефективних сплавів.
Схема виробництва (зліва) і порівняння характеристик нового сплаву з сучасними аналогами. Зображення: Andrew B. Kustas et al., Applied Materials Today
Інженери відзначають, що новий матеріал незвичайний тим, що жоден з металів не становить більше половини готового матеріалу і при цьому включає велику кількість різних металів. Для створення сплаву використовується спеціальна модель, заснована на відомих даних з металургії, яка дозволяє розраховувати і передбачати властивості готового матеріалу.
Більшість сучасних електростанцій — і ті, що працюють від викопного палива, і атомні станції – використовують тепло для обертання турбін, що виробляють електроенергію. Ефективність силової установки обмежена тим, наскільки високу температуру витримують металеві деталі турбіни. Чим вона вища, тим більше енергії може бути перетворено в електрику при одночасному зниженні кількості відпрацьованого тепла, що виділяється в навколишнє середовище.
Дослідники продовжать роботу з дослідження нового сплаву, щоб вивчити можливості масштабування виробничої технології та роботу сплаву в реальних умовах.