Хіміки розробили технологію отримання графену з викинутих автомобільних покришок: десятої частки відсотка такого матеріалу досить, щоб бетон став міцніший майже на третину.
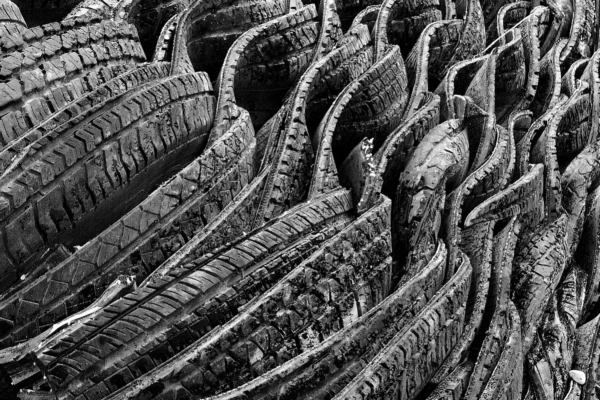
Щороку у світі викидають майже мільярд старих автомобільних покришок. Це сміття є серйозною глобальну проблему, і вчені шукають нові шляхи для перероблення та повторного використання матеріалів шин – в принципі з них можна отримувати навіть компоненти літій-іонних акумуляторів. А недавно хіміки з Університету Райса навчилися виробляти зі старих покришок графен – низькоякісний, але відповідний для додавання в цементний розчин і отримання з нього бетону підвищеної міцності.
Автори відзначають, що і сам бетон є помітне джерело парникових газів в атмосфері. Тому якщо використання більш міцних сортів дозволяє збільшити час експлуатації побудованих споруд, це теж послужить на користь навколишньому середовищу, до того ж заощадивши ресурси. Стаття з описом нового методу використання старих шин в бетоні опублікована в журналі Carbon.
Новинка спирається на «флеш» – технологію, яку Джеймс Тур (James Tour) і його колеги представили близько року тому. Вона дозволяє спалювати органічні відходи в потужних і коротких (від 0,3 до однієї секунди) електричних розрядах, перетворюючи їх в чистий вуглець. Атоми вуглецю утворюють графен з турбостратною – безпорядною, з великою кількістю дефектів – структурою. На відміну від «якісного» графену, він краще розчиняється, що полегшує деякі варіанти застосування.
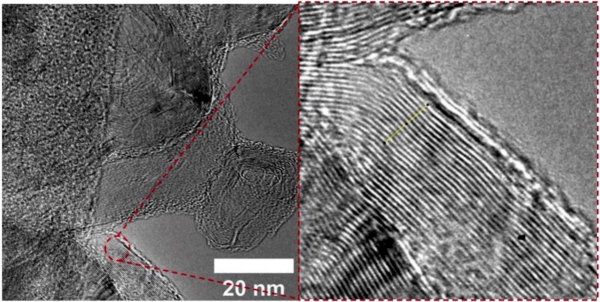
Тепер Джеймс Тур зі співавторами адаптували процес до перероблення старих шин. Сьогодні вуглецеві залишки, які утворюються після вилучення з них усіх цінних речовин, практично не приносять користі. Однак тепер їх можна обробляти електричними розрядами, перетворюючи до 70 відсотків вихідного матеріалу в турбостратний графен для додавання в цементний розчин. При використанні такого вуглецю в суміші з подрібненими шинами ця цифра становить близько 47 відсотків.
Далі вчені перевірили вплив «турбостратного” флеш “- графена» (tFG) на бетон, додаючи його в портландцемент в кількості від 0,1 до 0,5 вагових відсотків. Після застигання протягом всього лише семи днів матеріал продемонстрував на 30 відсотків більшу міцність на стиснення. За оцінками авторів, вартість процесу при промисловому застосуванні складе близько 100 доларів за тонну вихідного матеріалу.
Натхнення: naked-science.ru